Fermentation
Full integration from feedstock to product
At ABPDU, we offer a full suite of fermentation capabilities designed to accommodate the most challenging and cutting-edge applications in bioprocess engineering. Our capabilities in fermentation process development, piloting and scale-up, downstream processing, and analytical chemistry are designed from the ground up for flexible operation and process integration. Our experienced team of fermentation engineers is ready to assist with batch record development and technology transfer at any state of technology readiness.
Operational Modes
The ABPDU fermentation laboratory is equipped for aerobic and anaerobic fermentations in batch, fed-batch, or continuous configurations. Our equipment is highly customizable for advanced fermentation configurations including two-phase extractive fermentation, cell retention, chemostat operation, and volatile product capture.
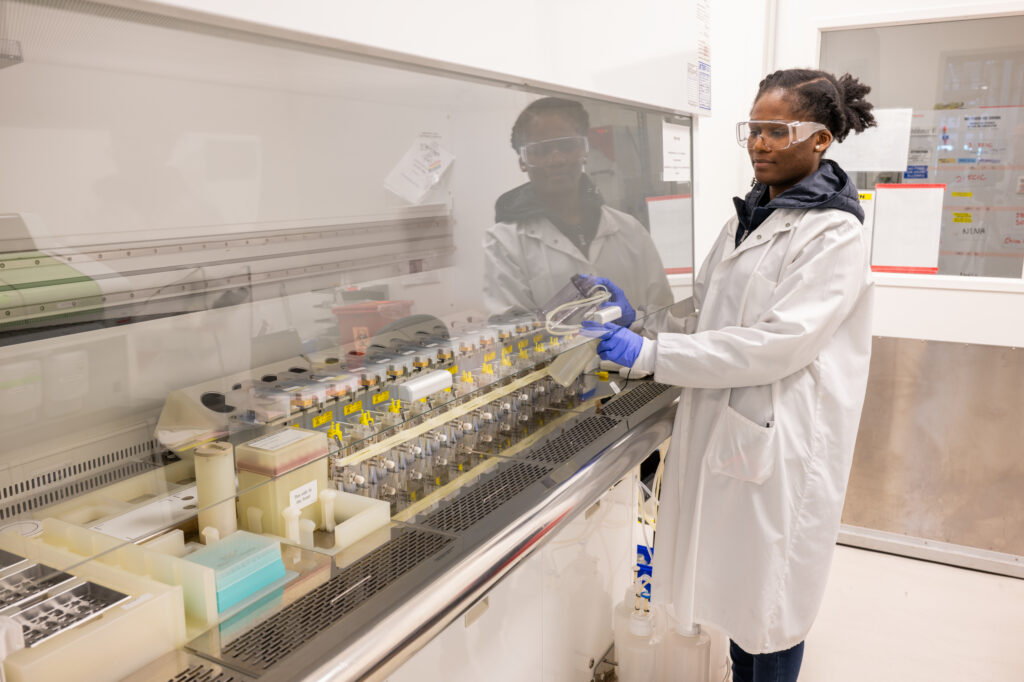
Host Organisms
We have experience with a wide variety of wild-type and recombinant hosts including bacteria, yeast, heterotrophic algae, and filamentous fungi. Our biosafety team will work closely with you to ensure smooth onboarding of novel processes with unique hazards.
Process Controls
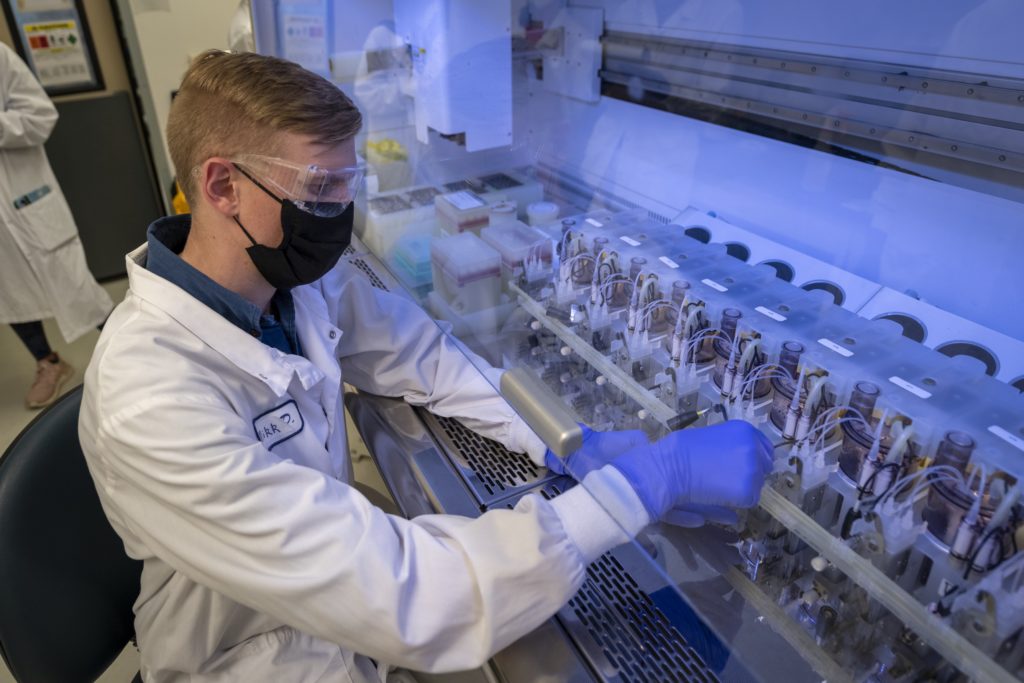
Our bioreactors are equipped with flexible process controls to enable remote monitoring and customizable feedback-based process controls, including automated induction timing and demand-based feed profiles.
Integrated Analytics
Our bioreactor systems are equipped for online monitoring of pH, DO, process weights, and respiratory gas profiles. These measurements can be combined with off-line analysis of metabolite profiles, nutrient profiles, substrate consumption, and cell health to compile a comprehensive analysis of fermentation performance.
Gas Fermentation
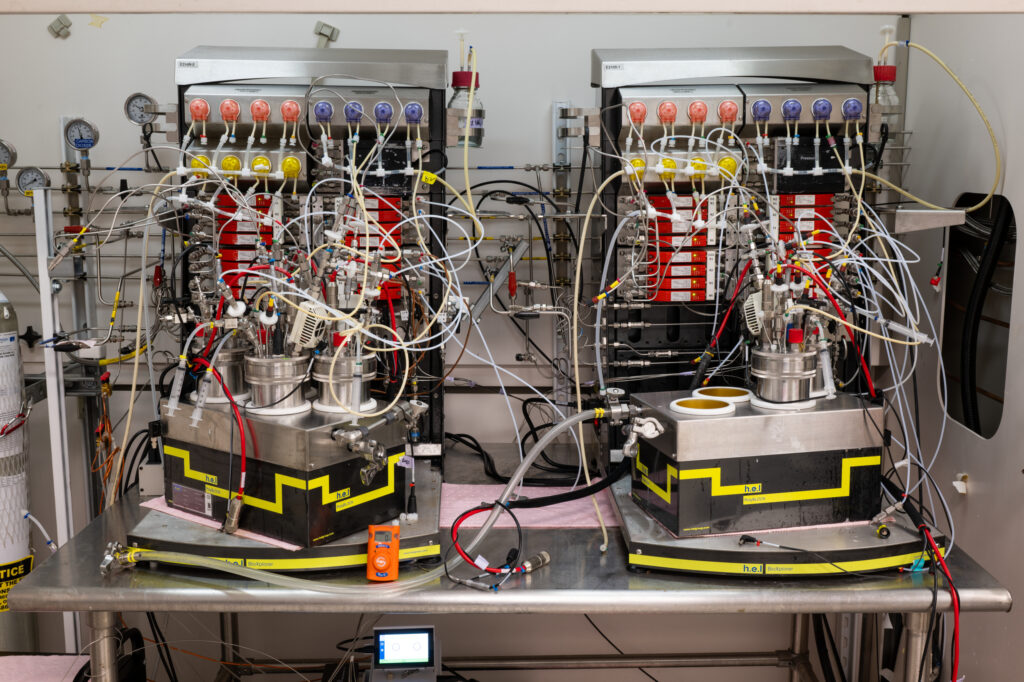
Using gaseous feedstocks is a compelling strategy to reduce feedstock cost. However, effective delivery of flammable gas to the fermentor presents significant challenges for conventional bioreactors. Our facility is well-equipped for safe experimentation with these feedstocks with a suite of 8 x 500 mL pressurizable gas fermentors, each equipped for customizable supply of carbon dioxide, hydrogen, methane, carbon monoxide, oxygen, and/or nitrogen.
Self-Driving Bioreactors
We are establishing scientific methods needed to accelerate fermentation process development in bioreactors by applying artificial intelligence and machine learning based methods. A bioreactor equipped with such technology will utilize real-time data and self-adapt ongoing fermentations towards better results. Such a bioreactor equipped by AI and ML methods — a self-driving bioreactor — has the potential to significantly improve testing efficiency and thereby expand testing to parameter space typically neglected due to resource constraints. At the commercial scale, self-driving bioreactors have the potential to minimize failure and maximize product yields, thereby delivering biofuels and products at competitive prices.
This new paradigm of biomanufacturing is necessary to reduce operating costs and compete with international manufacturers. The U.S. has a significant advantage in offering top quality utilities needed for biomanufacturing, such as clean water, uninterrupted power, etc. By reducing other operational costs, the U.S. has the potential to be a world leader in commercial biomanufacturing. Learn more about the specific projects.
Pilot-Scale Fermentation
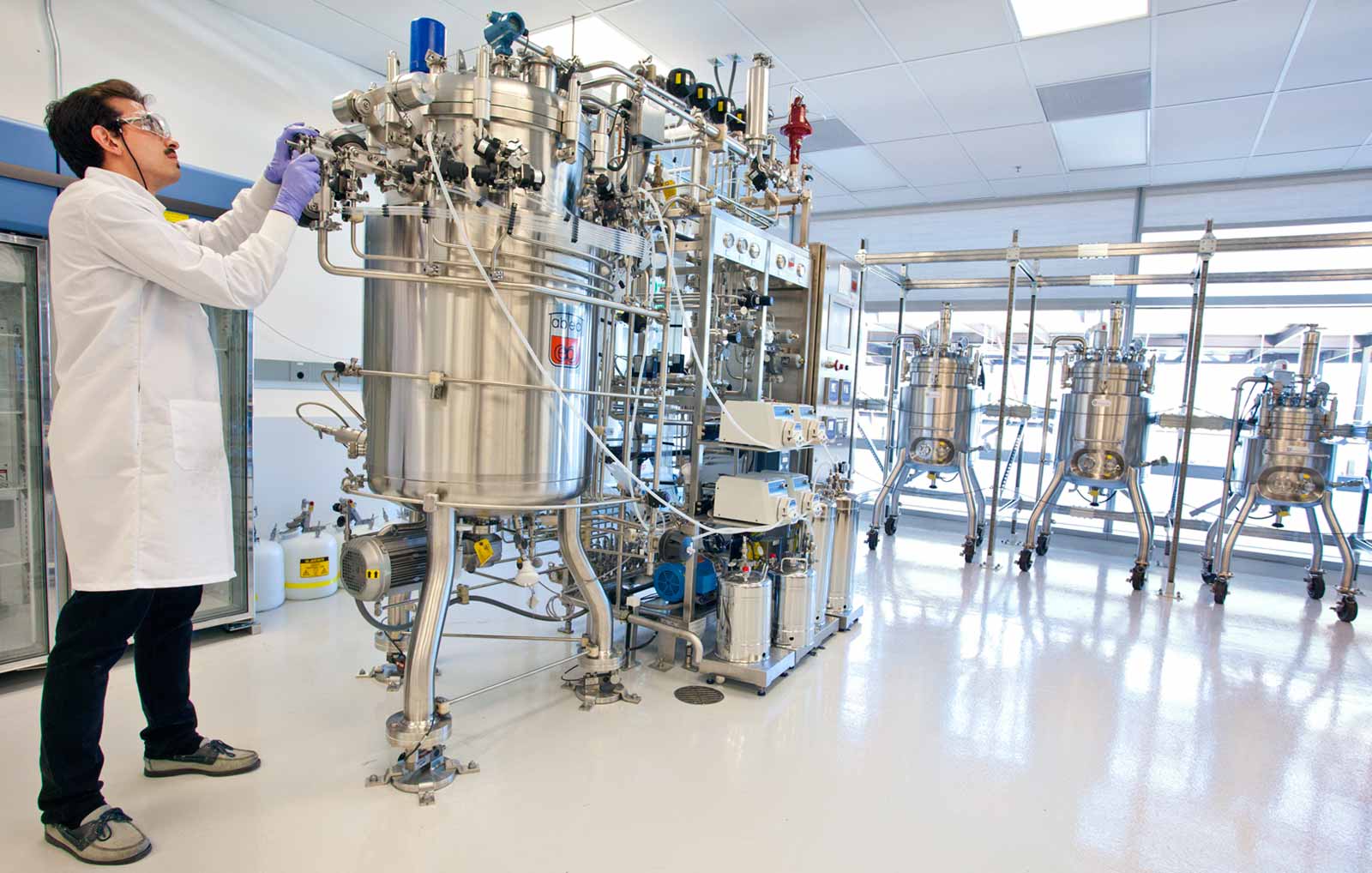
Our 300L ABEC bioreactors are the perfect size to evaluate process scalability, to produce larger product batches for potential customers, and to generate sufficient material to apply industrially relevant downstream processing techniques. A variety of processes demonstrated in our 300L bioreactors have successfully transferred to demonstration scale, and even directly to contract manufacturing.