Techno-Economic Analysis
We work with you to balance economics and sustainability.
Applying techno-economic analysis (TEA) at an early stage of technology development can provide key insights into process economics, allowing well informed down-selection of unit operations and process configurations. Analytical insight into process sensitivities can also help prioritize research efforts and generate key performance targets on the road to commercialization.
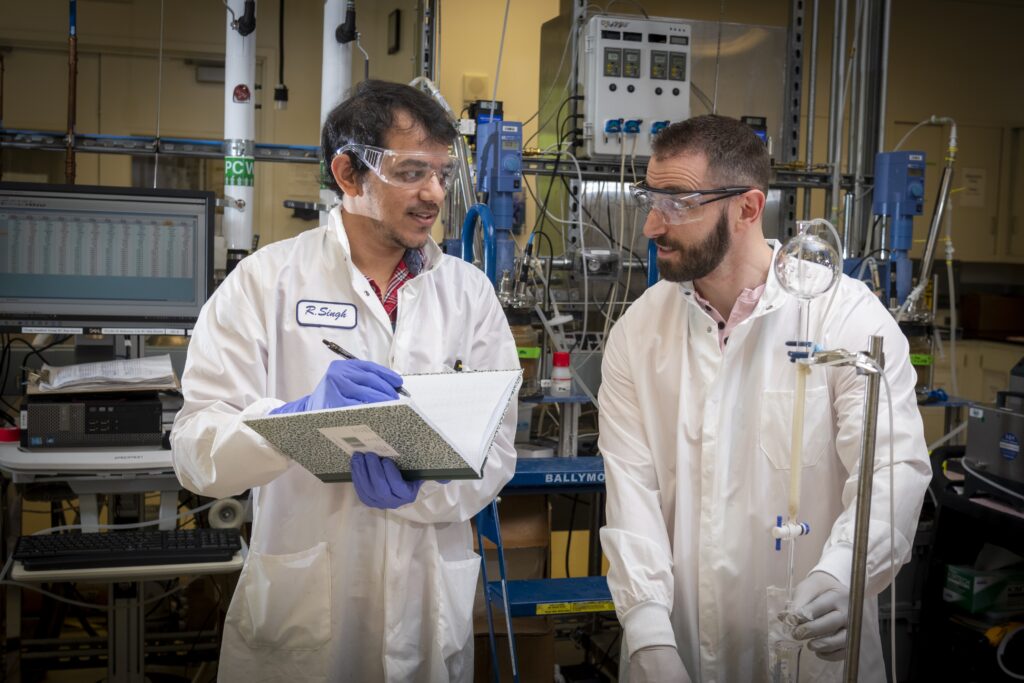
We are well-prepared to assist with early stage TEA. Our experienced team can convert preliminary process data into basic cost models, based on industry standard scale-up costs and process performance targets typical for your class of products. For more complex analysis, we can utilize SuperPro Designer to develop an integrated process model. These models provide a framework to evaluate mass and energy balances, itemize costs by unit operation, and assess the sensitivity of process economics to variable performance metrics and process configurations. At each step in the process, our staff can leverage their experience with dozens of previous collaborations to provide recommendations on technology options and to suggest potential areas for cost reduction via process optimization and intensification.
In addition to our in-house capabilities, ABPDU staff frequently leverage the resources and expertise of dedicated TEA and life cycle analysis research teams within Berkeley Lab, including bioprocess modeling experts within the Joint BioEnergy Institute. For rapid analysis, JBEI’s Life Cycle and Agronomy Division maintains a variety of cloud-based tools to assist with preliminary TEA, facility siting, and technology selection for bioprocess separations.