Saccharification
Achieving maximum sugar yield.
Saccharification — the process of converting cellulose and hemicellulose into fermentable sugars — is a considerable cost in the biomass to bioproduct pipeline.
We take the following factors into consideration:
- Biomass composition
- Type of pretreatment
- Dosage and efficiency of the hydrolytic catalyst or enzymes
We integrate pretreatment and saccharification to establish the optimum process parameters and selection of methodologies.
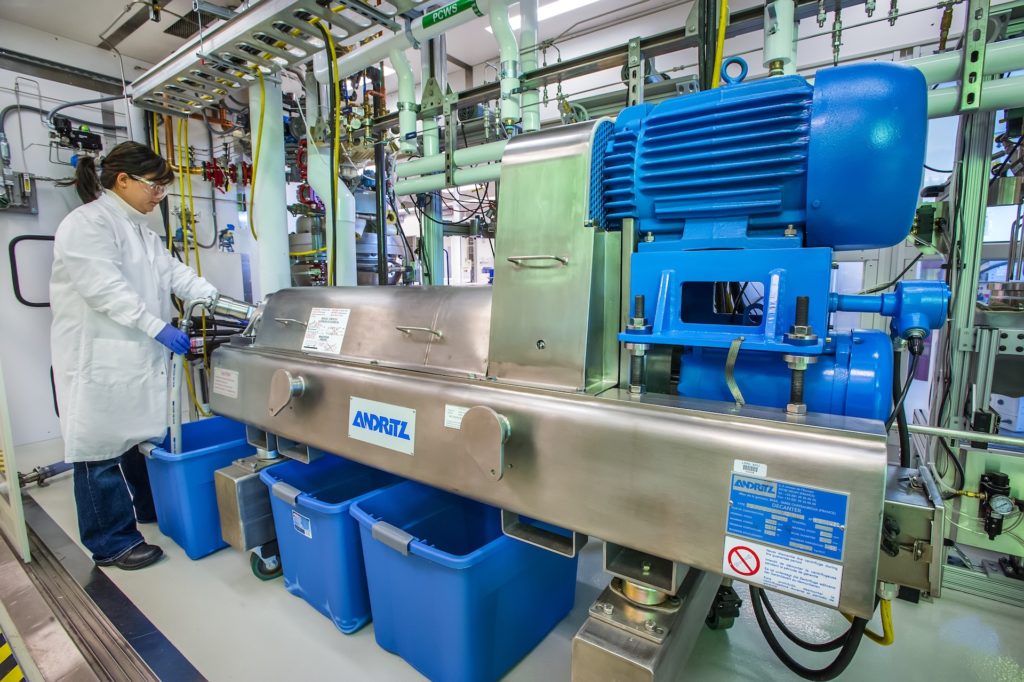
Saccharification Process Options
Cocktail Optimization of Enzymes
As the severity of the pretreatment process decreases, there is a corresponding decrease in the sugar yield after enzymatic hydrolysis. To maximize sugar yields from from cellulose and hemicellulose components of the pretreated biomass, a combination of various enzymes and increased enzyme dosage are necessary We offer a cocktail of enzymes such as cellulases, hemicellulases, and other supplementary enzymes to ensure hydrolysis.
High Solids Enzymatic Hydrolysis
Maintaining high solids concentrations throughout the biomass conversion process is important for optimizing final product titers while minimizing the intensity of separation processes. High substrate concentration results in a highly concentrated sugar solution, which is beneficial in separation processes after fermentation. The extent to which solids loading can be increased in hydrolysis is dependent on factors such as the type of feedstock, the pretreatment process, and the specific enzyme or catalyst being used.
Solid/Liquid Separation
After saccharification, the lignin-rich solid is separated from the sugar-rich aqueous phase through a combination of centrifugation and filtration techniques. The solid residue could be used for lignin valorization or other applications.
Mass/Energy Balance
A mass balance, also called a material balance, is a comprehensive accounting of all materials entering and exiting a system. Mass balance is essential to establish a process as it is required to calculate the actual conversion of feedstock, monitor process flow, identify limitations or bottlenecks, and model large-scale processes within desired reactors. Similarly, an energy balance can be established across a process by assuming that net energy loss from a reactor is negligible.