Purification & Advanced Recovery
We extract the most value from your starting material.
In a biochemical conversion process, the highest costs can often be found in the area of downstream processing—recovering and purifying the product after production.
Whether we’re extracting products according to your specifications, performing third party validations, or testing your concept, our broad depth of knowledge of the industry enables us to extract the most value from the starting material.
Unique Specifications for Unique Processes
Each product and intermediate has unique physical and chemical properties. Several factors can further compound the uniqueness factor. In some cases, a single recovery step is not sufficient and will require the development of a recovery process chain.
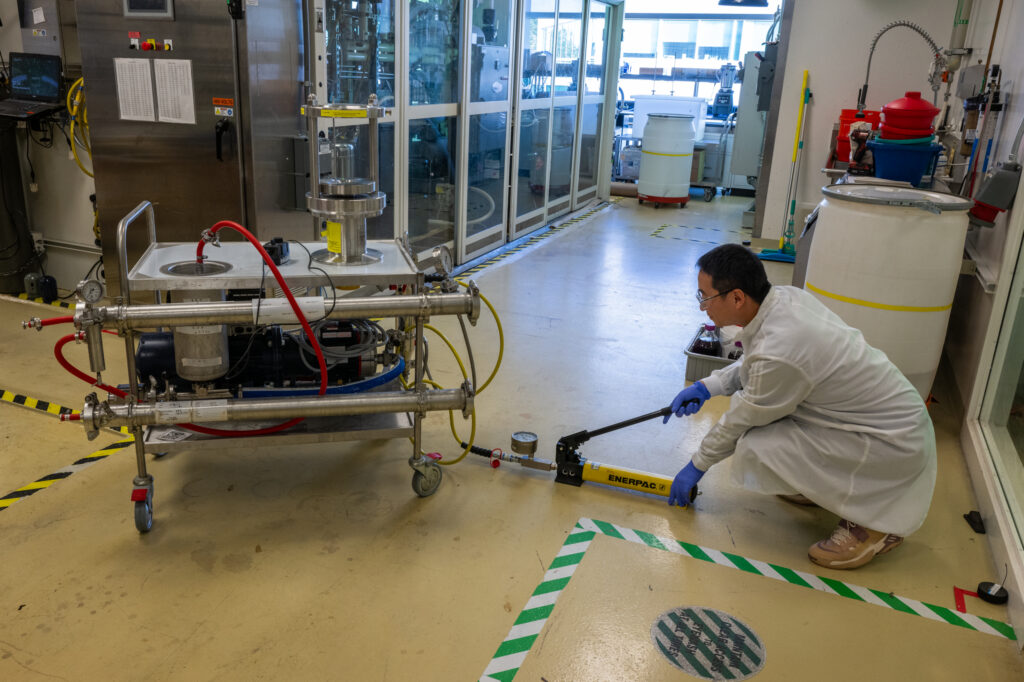
Designed to Enhance Yield and Quality
We define specific recovery and purification steps based on your final product specifications. Our team will explore any optimizations that could enhance recovery yield and product purity. For example:
- Each product can require different process parameters
- Each feedstock can lead to different separation and recovery processes
- Stepwise yields can be individually optimized
- Reagents can be substituted to decrease the cost factor
Purification & Advanced Recovery Process Options
Continuous centrifugation
Once a conversion or upgrading process is complete, continuous centrifugation is an excellent way of separating at high throughput. With continuous centrifugation, the disk stack separator separates solids from liquids in one continuous process. This piece of equipment is capable of handling flow rates of 100L/hr, making the processing of various biologicals smooth and virtually effortless.
Volatile Product Capture
The ABPDU is able to isolate volatile products directly from the fermentation headspace, through the use of a stripping column. For compatible products and processes, such an approach can be a rapid method for producing enough material for functional testing and evaluation of physical properties. It can also be an important consideration for understanding the facility and process development needs for future, dedicated, commercial scale facilities.
Tangential flow filtration
Tangential flow filtration (TFF) is a rapid and efficient method for separation and purification of biomolecules. Your biomolecule of interest, or product, can be retained and separated from other low molecular weight contaminants, or it can be passed and purified from higher molecular weight contaminants and particles.
TFF can be used to concentrate and desalt sample solutions ranging in volume from 10 mL to thousands of liters. It can be used to fractionate large from small biomolecules, harvest cell suspensions, and clarify fermentation broths and cell lysates. At ABPDU, we have a continuous TFF at a feed flow rate of 4.5 mL/min that can separate biomolecules to up to 10 kDa.
Pilot-scale chromatography protein purification
One of the biggest challenges in protein purification is minimizing time and maximizing yield. To overcome these challenges, purification seeks to find the least amount of steps to produce purified product most efficiently. The best way to accomplish these goals is to conduct small scale experiments which scale effectively. The AKTA Avant 150 system at the ABPDU is the perfect instrument for this task due to its wide adaptability to many column chemistries and suitability for purification optimization.
Bulk freeze drying
In bio-separations, freeze-drying–or lyophilization–can also be used as a late-stage purification procedure, because it can effectively remove solvents. Furthermore, it is capable of concentrating substances with low molecular weights that are too small to be removed by a filtration membrane. Freeze-drying is often reserved for materials that are heat-sensitive, such as proteins and enzymes. The low operating temperature of the process leads to minimal damage of these heat-sensitive products.
Flow-through sonication and homogenization
Ultrasonication is an effective means to break cell structures and allows for the processing of high-concentration and high-viscosity slurries. The option of producing high-viscosity slurries upfront allows for reducing the volume to be processed, reactor sizes both in the upstream and downstream ends of the process chain. Thereby, ultrasonic disintegration is an excellent recovery option for process intensification throughout the process chain and can be easily tested in any scale.