
Bay Area startup Oobli (formerly Joywell Foods) has developed a fermentation process that produces sweet proteins, which mimic the taste of sugar without the adverse health effects.
Not only do traditional sugar and most non-nutritive sweetener alternatives have bad implications for health, sugarcane farming requires millions of acres of land. Producing sweet proteins via fermentation offers a more sustainable solution, said Oobli CEO Ali Wing.
The company teamed up with ABPDU seeking to scale up production of their sweet proteins. Together, the teams completed three successful piloting campaigns and optimized Oobli’s process for further scale-up and commercialization readiness.
Tina Wang, Director of Program Management at Oobli, said the collaboration also helped them accelerate their process development.
“ABPDU has more bench power and high throughput equipment to help startups like us that have fewer resources in terms of people and equipment,” she said. In particular, Wang said ABPDU’s expertise in running experiments with the Sartorius Ambr® 250 was vital for improving their strains and that the support of an extended, expert team is always welcomed.
One aspect of the collaboration that stood out to Wang was the open line of communication and ABPDU’s ability to tailor the project to their needs.
“If we want to tweak something that’s out of the standard process, ABPDU’s team is really willing to work with us on customizing our process and workflow,” she said. “That stands out among other facilities I’ve worked with.”
Wang also noted that Oobli’s team has appreciated being able to actively participate in the development of their process alongside ABPDU’s team.
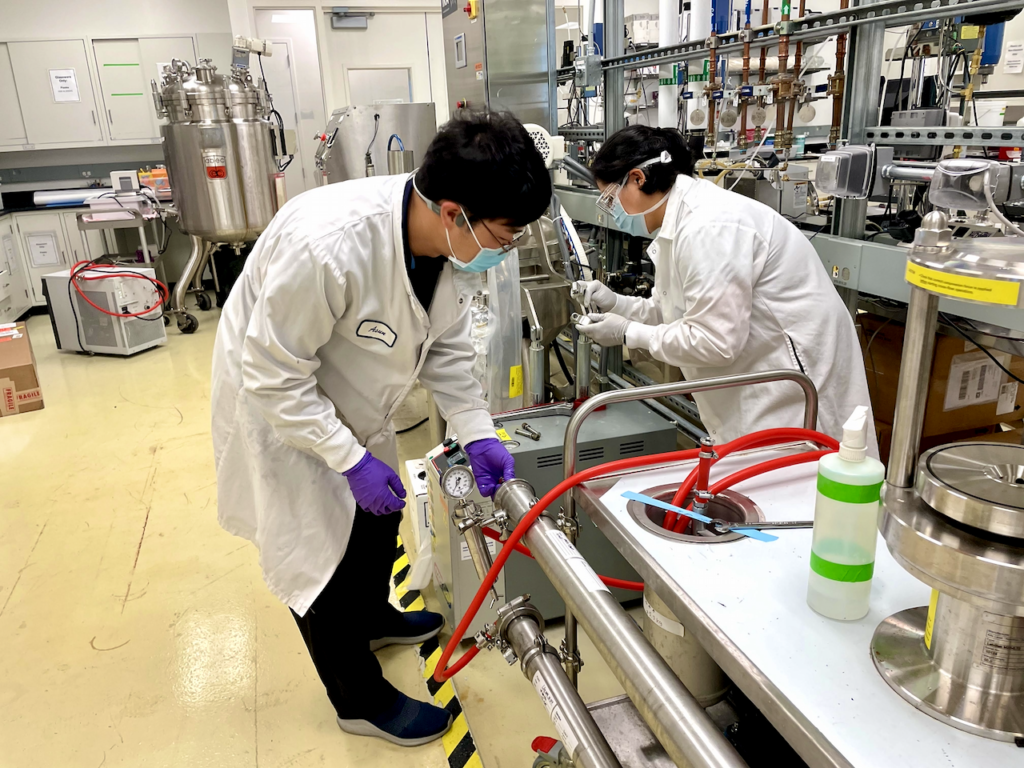
“They allow us to be hands-on in the facility,” Wang said. “In that aspect, ABPDU is more of a teaching facility in which we really get our hands dirty and learn the process as we go.”
Jason Ryder, Co-founder and CTO of Oobli said that as time goes on, this knowledge only becomes more valuable to their company.
“Our work with ABPDU provided Oobli with an opportunity to perform our first tech transfer, scale-up, and third party demonstration of our sweet protein production process,” said Ryder. “This sets us up for success as we continue to develop, scale, and commercialize our technology platform and products.”
The project has been a learning experience for ABPDU’s team as well, said David Chang, process engineer at ABPDU and project lead for the collaboration.
“This project contains almost all aspects of bioprocess development, including process development at the bench scale, process verification at pilot scale, and downstream separation and purification,” Chang said. “This provides us at ABPDU with a very comprehensive learning experience and helps us continue to serve the community better.”
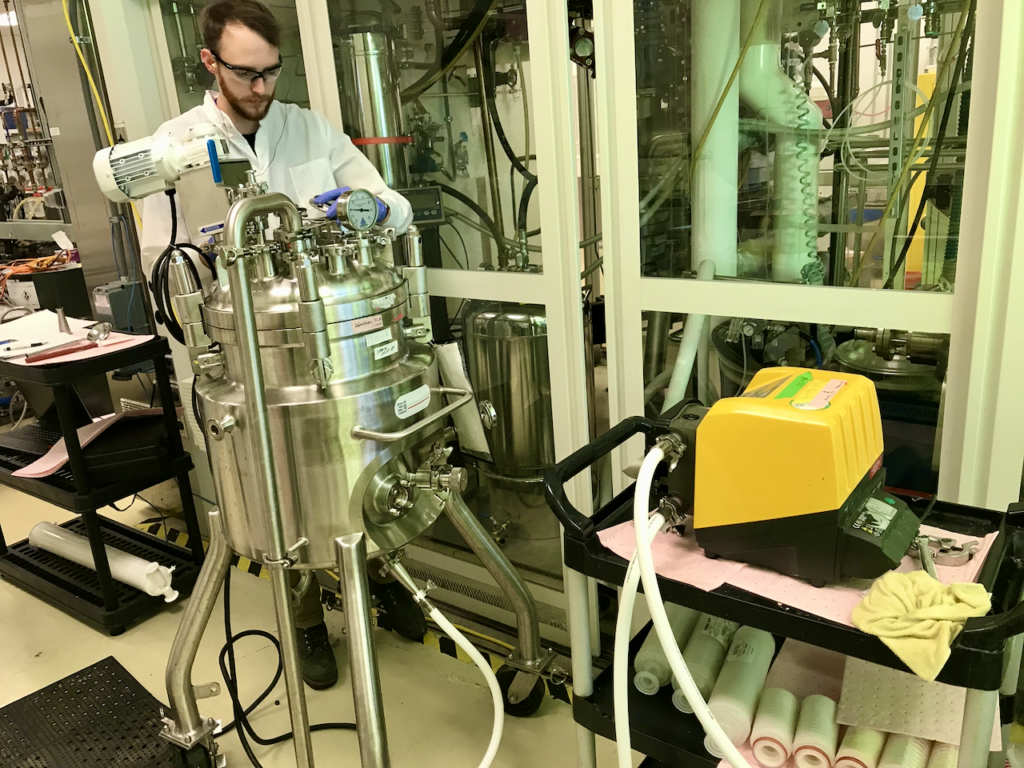
Asun Oka, a process engineer at ABPDU who led the collaboration’s downstream recovery, said the project was an opportunity to bridge the gap between research and production.
“With lab members working side by side with Oobli, not only were we able to share our experiences but also learn about the intricacies in the differences of scale and design,” Oka said. “It brings me joy to know that ABPDU was able to assist Oobli in the development of their process and that we will continue to work with them to see how these kinds of collaborations cultivate the bioeconomy.”
So far, ABPDU has scaled up production of two of Oobli’s sweet proteins, but the company has several other candidates lined up on their sweet protein platform. As Oobli prepares to launch their first beverage product, they’ll continue coming back to ABPDU for process development of their other sweet proteins and products in the pipeline.
“We greatly appreciate the high level of collaboration, technical expertise, and partnership with our colleagues at ABPDU. We look forward to coming back to Emeryville again and again — whether it’s testing new strains, optimizing our fermentation and downstream process, or simply establishing proof of concept before we move to larger scale,” Ryder said.
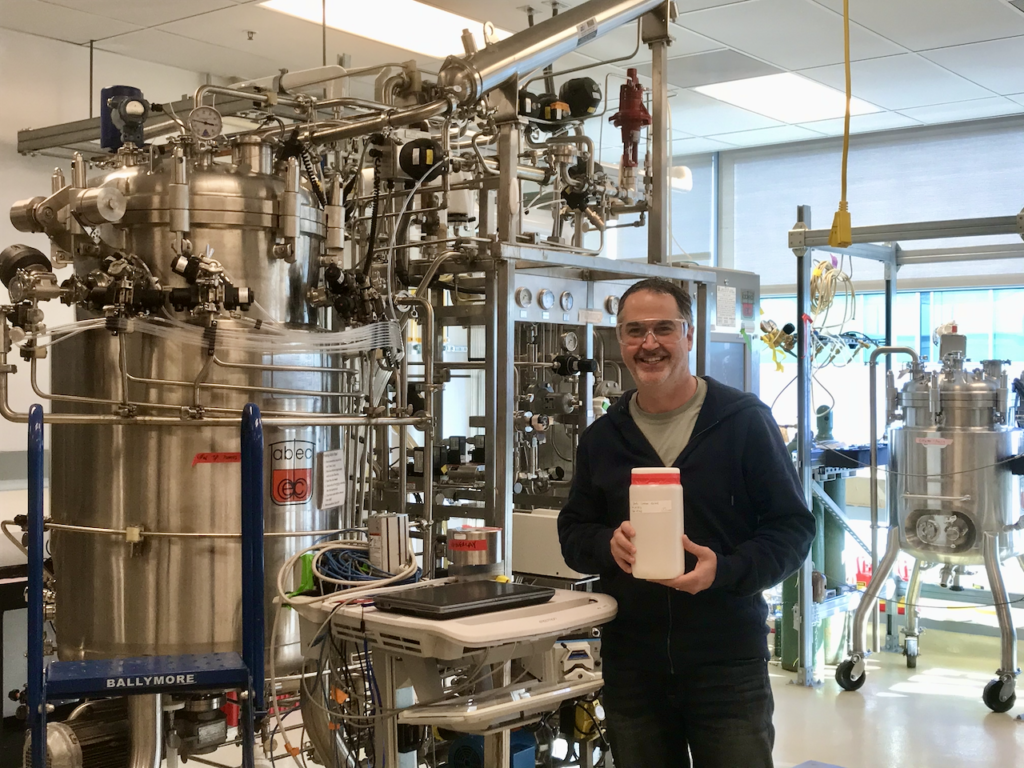