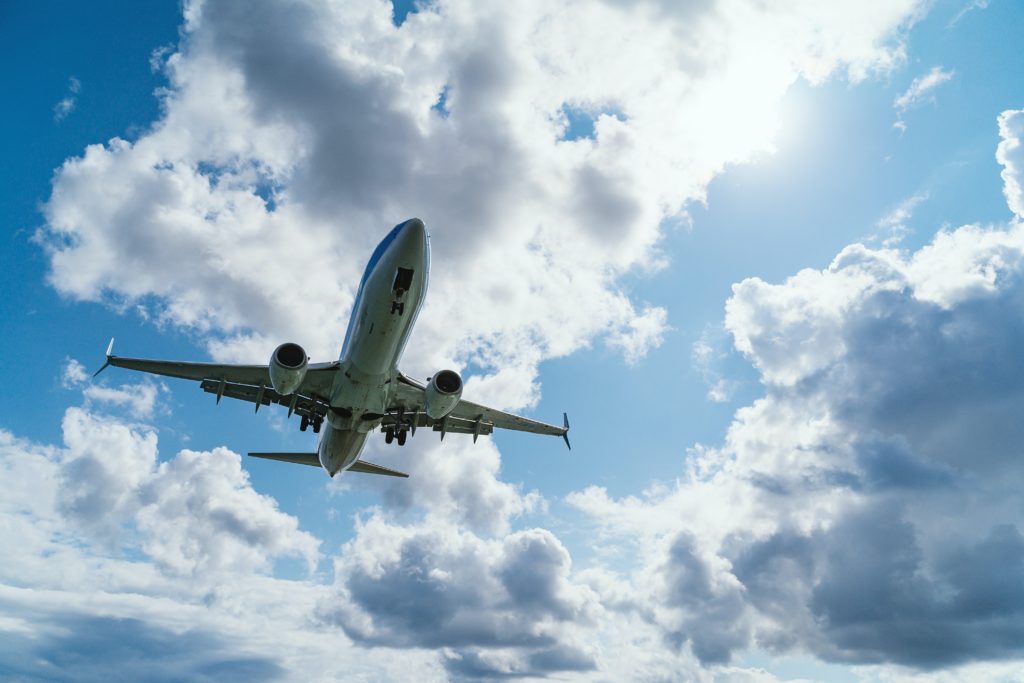
Sustainable aviation fuels are increasingly in demand, as they are comparable in performance to traditional jet fuels but reduce greenhouse gas emissions and can be made using renewable resources.
However, producing these fuels is a tricky biological process. Some important aviation fuel molecules are volatile, meaning they evaporate at room temperature. During the fermentation process, these volatile molecules leave the fermenter as a gas, and then must be recaptured.
“We began to notice this as a challenge that hadn’t been addressed much in this industry,” said Eric Sundstrom, research scientist at the Advanced Biofuels and Bioproducts Process Development Unit (ABPDU), a research facility funded by the U.S. Department of Energy’s (DOE’s) Bioenergy Technologies Office (BETO).
ABPDU collaborated with BETO’s Bioprocessing Separations Consortium and researchers at Argonne National Laboratory (ANL) to develop new experimental setups and technologies to advance volatile product capture. This collaboration allowed ABPDU to develop capabilities and expertise to safely deploy off-gas capture for real-world fermentations. “We first designed a recovery system at the bench scale,” said Carolina Araujo Barcelos, senior fermentation engineer at ABPDU. “We used the knowledge we obtained at this scale to design a large-scale system with 25-fold higher capacity.”
The research facility then partnered with Amyris Inc., a leading synthetic biology company that is accelerating the beauty, health and wellness markets to sustainable consumption through its Lab-to-Market technology platform. Amyris pioneered molecular bioengineering and process development for biofuel in the early 2000’s, and retains expertise with terpene molecules used in the making of fragrances but also sustainable aviation fuel blends.
“ABPDU’s equipment is able to validate our production models at bench scale,” said Adam Meadows, principal scientist at Amyris. “Together, our teams were able to produce and purify terpene samples that had energy densities comparable to leading jet fuel formulations, which is very exciting.”
“ABPDU’s team executed the fermentation extremely well,” Meadows said. “We achieved even better performance at the 300-liter scale than we did at our bench scale. This project has been a success in terms of results and the level of collaboration and support from ABPDU’s team has been exceptional.” ABPDU aims to continue to provide their off-gas capture capability to other partners interested in volatile product capture.
“This system can be used to recover any volatile compound,” Barcelos said. “It also benefits the downstream process by increasing the product concentration and reducing the impurity and the final volume that needs to be processed, which saves time and money.”
Sundstrom said ABPDU has evolved to become a leader in volatile product recovery. “It’s rewarding to be able to respond successfully to a separations challenge that we’re seeing more and more often in industry, and to apply our expertise to scale up sustainable aviation fuels,” Sundstrom said.